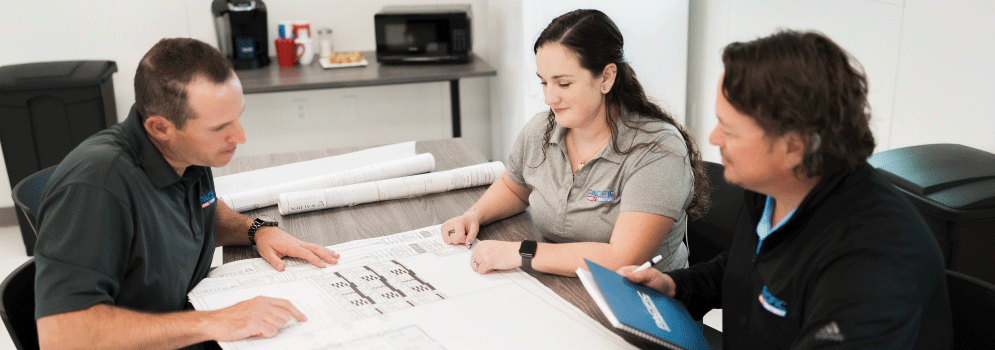
10 Steps to a Successful Modular Construction Project
In the ever-evolving world of construction, modular construction is rapidly becoming a popular choice for many developers and contractors. Its efficiency, cost-effectiveness, and environmental benefits make it an appealing alternative to traditional building methods. If you’re considering a modular construction project, follow these ten essential steps to ensure success.
Define Your Project Goals
Before embarking on any construction project, it’s crucial to establish clear goals and communicate them to your modular construction provider. Determine the purpose of your modular building, whether it’s for residential, commercial, or industrial use. Define your budget, timeline, and any specific requirements or constraints. Having a well-defined plan will guide every subsequent decision and help keep your project on track.
Design and Plan Thoroughly
Collaborate closely with your modular construction partner during the design phase. Utilize their expertise to optimize the design for modular construction, considering factors such as transportation, assembly, and site-specific requirements. Thorough planning will help identify potential challenges early and allow for efficient problem-solving.
Obtain Necessary Permits and Approvals
Modular construction projects, like traditional stick-built methods, require various permits and approvals. Work with your construction partner to navigate the regulatory landscape and ensure all necessary documentation is in place. This step is crucial to avoid legal issues and project delays.
Prepare the Construction Site
While your modular units are being fabricated off-site, work with your modular construction partner to coordinate the preparation of the construction site. This involves site clearing, grading, and laying foundations. This also includes ensuring all utilities are in place and that the site is ready for the arrival of the modular components. Proper site preparation is vital for a smooth assembly process.
Focus on Quality Control
Quality control is paramount in modular construction. It’s crucial to work with a partner that establishes strict quality assurance processes during the fabrication of the modular units and inspects each unit before it leaves the factory to ensure it meets all design and safety standards. Working with a modular construction company that maintains high-quality standards will result in a better final product.
Efficient Transportation and Delivery
Transporting modular units requires careful planning and coordination. Ensure that your construction partner has experience with logistics and transportation. If they do, they’ll plan the delivery routes, secure any necessary permits for oversized loads, and schedule the transportation to minimize disruptions and delays.
Assemble On-Site
Once the modular units arrive at the construction site, the assembly process begins. This step involves connecting the modules, installing utilities, and completing any necessary finishing work. A well-coordinated assembly process can significantly reduce construction time and costs compared to traditional methods.
Conduct Thorough Inspections
Before finalizing the project, conduct comprehensive inspections to ensure everything is up to code and meets your specifications. This includes checking structural integrity, electrical systems, plumbing, and overall safety. Address any issues promptly to avoid future problems.
Finalize and Handover
The final step is to complete any remaining work, such as landscaping or interior finishes. Typically, your modular provider will complete the interior finishes, and they can also complete the landscaping. To complete the handover, your modular construction partner will ensure all documentation, warranties, and manuals are provided to you.
Choose the Right Modular Construction Partner
Selecting a reputable and experienced modular construction company is critical. Look for a partner with a proven track record in delivering quality modular projects. Check their portfolio, read client testimonials, and ensure they have the necessary certifications and expertise in your specific type of project.
As a family-owned and operated company with over 40 years in the industry, Pacific Mobile Structures works with you in a way that’s unique compared to other modular construction providers – with a relentless, customer-first commitment. Whether you need to lease a relocatable modular office or purchase a new, custom-built structure, it is reflected in every dealing with you. From the condition of our modular buildings to our staff talent, to the speed and ease with which you receive our buildings.
Reach out to our team today to get started on your next project tomorrow. Large enough to deliver on big, custom modular construction projects almost anywhere in the western U.S. and Texas. Because we’re family-owned and privately held, you’ll never catch us cutting corners or compromising on service to please shareholders.