Modular construction: A smarter way to build.
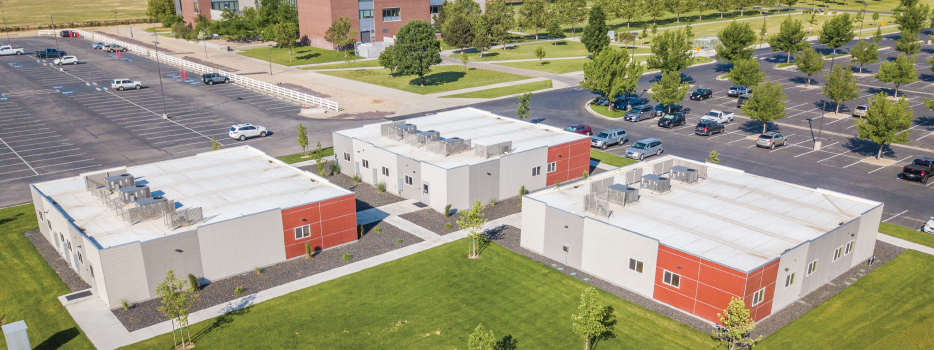
What is modular construction?
In modular construction, sections of a building (that is, modules) are built in the controlled conditions of a factory, then transported to the building site and assembled there to create the finished structure. Contrast this with conventional site-built construction, where all of the individual building materials are trucked to the site and the entire construction process takes place there.
Factory construction allows better quality management with the application of rigid protocols and rigorous testing. Each modular subassembly is engineered to withstand the stresses of transportation and being craned onto a foundation. Once assembled and sealed, they become one integrated wall, floor, and roof assembly that is generally stronger than an equivalent site-built design.
Moreover, with approximately 80% of construction activity moved from the site location to the factory, there is significantly less vehicle traffic and general site disruption. This is especially valued at sites that need to operate with a normal level of activity throughout construction, such as in healthcare and education. Schools especially value modular because the compressed timeframes often allow the entire project to be completed over the summer in time for fall classes.
Learn more about modular construction and the top 10 reasons for using modular construction methods.
Compared to site-built construction, the modular method is:
Green
Fast
Smart
Common modular myths debunked
"Site-built structures are built better"
"Modular buildings aren't aesthetically pleasing"
"Modular buildings are only temporary"
Request a Quote
Whether you know exactly what you want or could use some guidance, we’re ready to help. You can get in touch with us however you prefer.