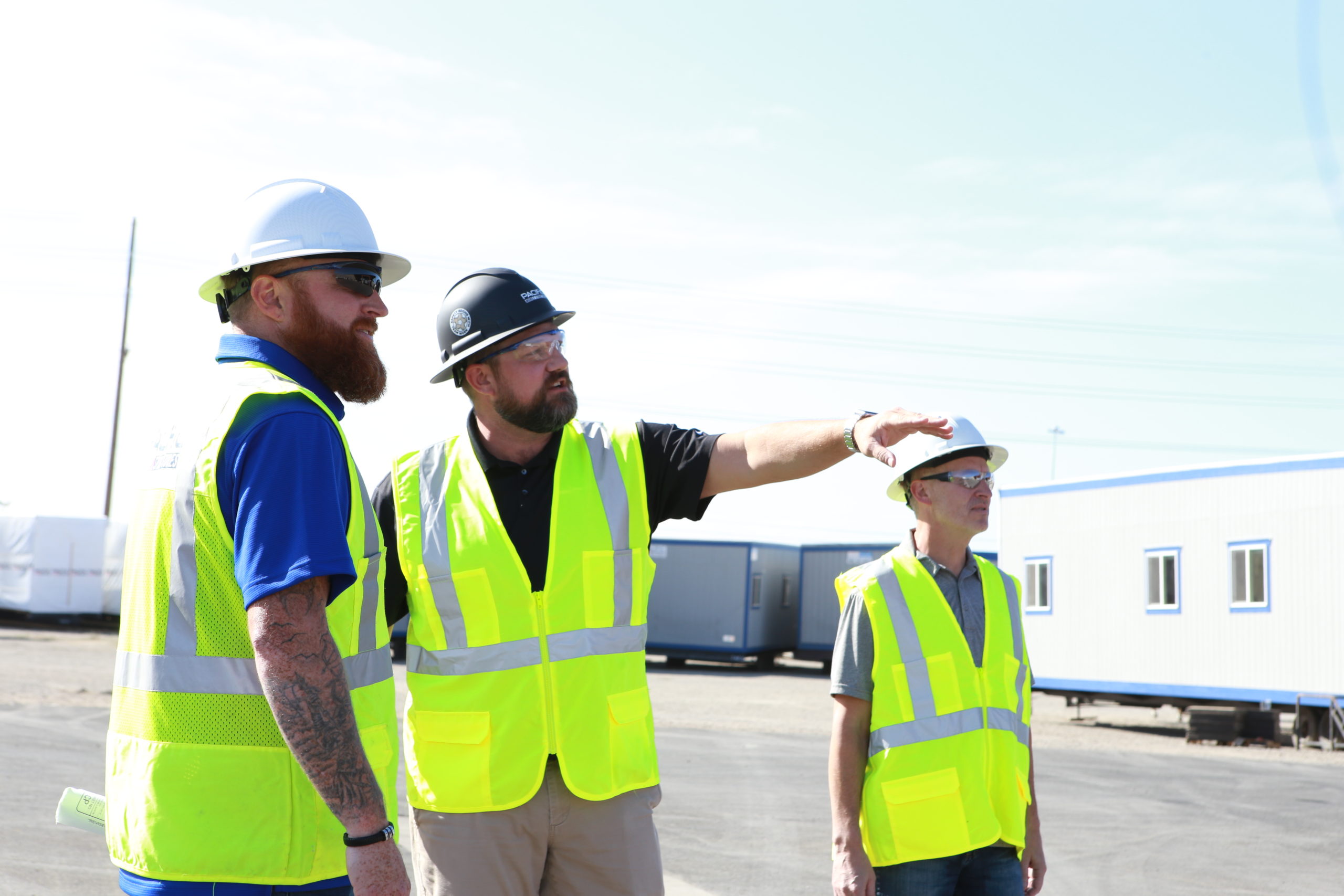
Breaking Down Barriers: Overcoming Misconceptions about Modular Structures
Modular construction has been gaining momentum in recent years as a cost-effective, efficient, and sustainable alternative to traditional building methods. Despite its rising popularity, several misconceptions surround this innovative construction approach. Yet, despite its undeniable benefits, modular construction remains shrouded in myths and misconceptions that deter many who would greatly benefit from its innovative approach.
So, let’s do some myth-busting, shall we?
Myth #1: It’s a New Construction Method
Many people believe that modular construction is a newer way of building, but it’s a construction method that dates back to ancient Rome. We’ve all heard the phrase “Rome wasn’t built in a day,” but it was built in less days than it could have taken because the Romans employed modular construction.
Myth #2: Modular Construction is Limited in Design Options
Some believe that modular buildings are plain and lack the design flexibility offered by traditional construction. However, this couldn’t be further from the truth. Modular construction allows for a wide range of architectural designs, finishes, and customization options. Advanced technology and engineering capabilities enable the creation of aesthetically pleasing and unique modular structures that cater to various preferences and requirements. In many instances, you can do more with modular construction than with traditional building methods.
Myth #3: Modular Buildings Lack Durability
There’s a misconception that modular structures compromise on durability and longevity. In reality, modular buildings actually have stricter code requirements than traditional stick-built buildings do. Modular components are precision-engineered in controlled factory environments, reducing the risk of errors and ensuring high-quality construction materials. Additionally, the controlled manufacturing process enhances the overall structural integrity of modular buildings, making them durable and resilient. Plus, modular buildings must withstand transport, which means they’re often built to a higher standard than stick-built structures.
Myth #4: Limited Size and Scalability
Another common misconception is that modular buildings are suitable only for small or temporary structures. In truth, modular construction is highly scalable and can be applied to projects of varying sizes, from single-family homes to large commercial buildings. The modular approach allows for efficient replication of units, making it easy to scale up or down based on project requirements.
Myth #5: Slower Construction Time
Contrary to popular belief, modular construction significantly reduces construction timelines. Since modular components are manufactured off-site concurrently with on-site preparation, the overall construction process is expedited. This simultaneous approach ensures that projects are completed faster than traditional construction, minimizing downtime and reducing labor costs.
Myth #6: Modular Buildings Aren’t Up to Code
One prevalent myth surrounding modular construction implies that these buildings do not meet the stringent building codes and regulations applied to traditional stick-built structures. In reality, modular constructions adhere to the same, if not higher, building standards. The controlled environment of the manufacturing process ensures precision and consistency, with each module undergoing thorough inspections to comply with local and international building codes. Collaborative efforts with regulatory bodies further ensure that modular structures not only meet but often exceed the specific requirements of the regions they are constructed in.
Fact: Modular Construction is the Future of Construction
The misconceptions surrounding modular construction have obscured its true potential for too long. More and more, people are becoming aware of the undeniable advantages that modular construction brings to the table – from cost-effectiveness to sustainability and beyond. Replace myths with facts and embrace the future of construction with confidence, knowing that modular construction is not just breaking down barriers, but paving the way for a more efficient, adaptable, and sustainably built future.
Interested in stepping into the future and going modular for your next project? Contact our team and request a quote today.