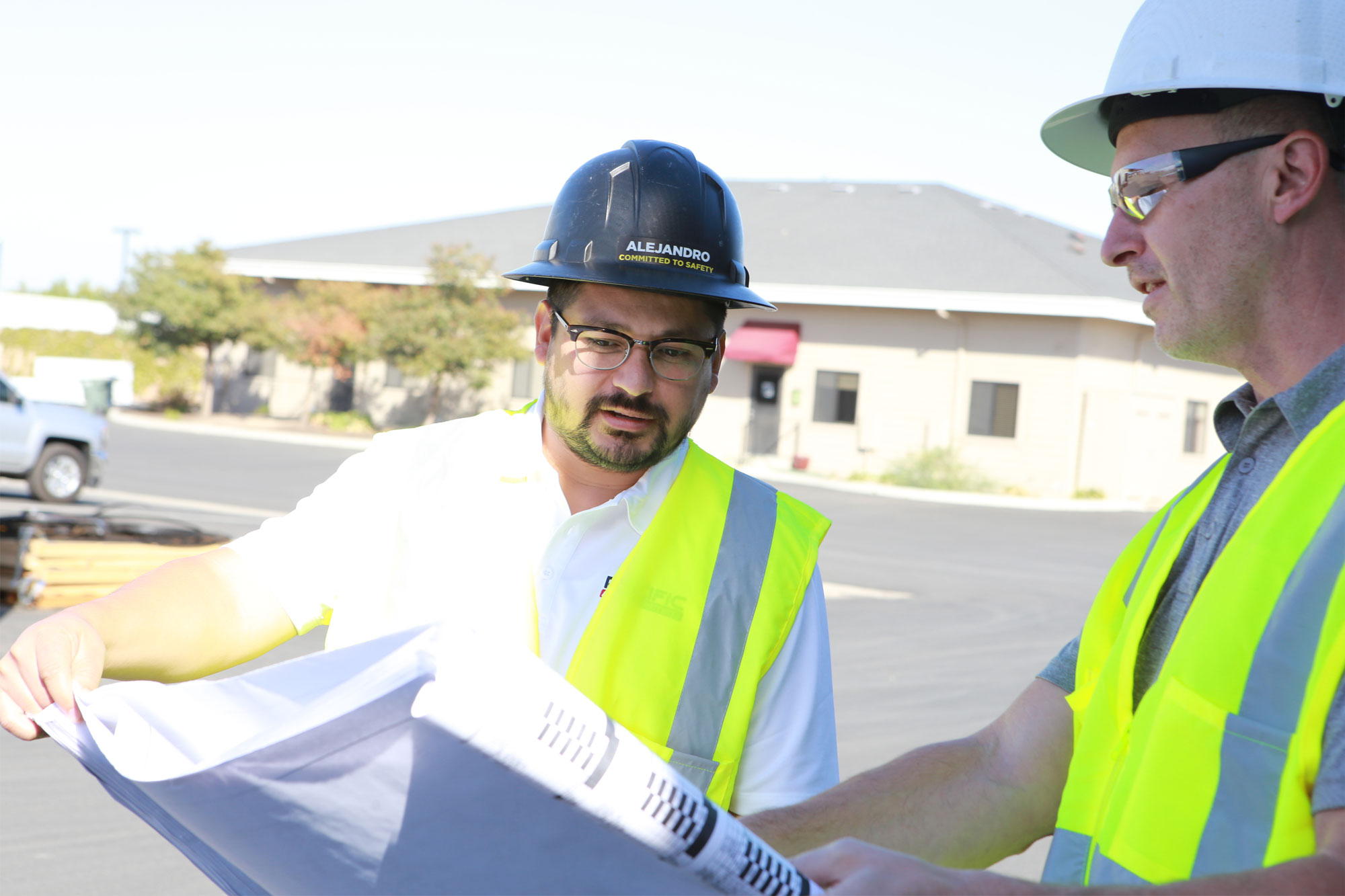
From Concept to Completion: The Modular Construction Process Explained
1. Understanding Modular Construction
What is Modular Construction?
Modular construction is a revolutionary building method where structures are constructed off-site in a controlled factory environment. Buildings are divided into modules, which are then transported and assembled on-site. This method differs from traditional construction by utilizing a more systematic and streamlined process.
Advantages of Modular Construction
Time and Cost Savings: One of the key advantages of modular construction is the significant reduction in project timelines. With simultaneous on-site preparation and module manufacturing, projects can be completed up to 50% faster than traditional construction methods. Additionally, the controlled environment of a factory reduces the likelihood of weather-related delays.
Reduced Environmental Impact: Modular construction is inherently more sustainable than traditional methods. The controlled factory environment minimizes waste, and materials can be recycled or reused. Moreover, the shorter construction time translates to reduced energy consumption and lower emissions, contributing to a smaller carbon footprint.
Enhanced Quality Control: The factory-controlled setting ensures that each module adheres to strict quality standards. With skilled professionals overseeing every step of the manufacturing process, modular construction consistently delivers high-quality, precision-engineered components. This results in a final product with fewer defects and a higher level of structural integrity.
2. Planning Your Modular Project
Conceptualization
Before diving into the planning phase, clearly define the purpose and scope of your modular construction project. Consider factors such as the intended use of the building, design preferences, and any specific requirements. This conceptualization phase lays the foundation for a successful project by aligning your vision with practical considerations.
Budgeting
While modular construction is known for its cost-effectiveness, it’s crucial to establish a realistic budget. Evaluate the total cost of the project, including design, manufacturing, transportation, and on-site assembly. Factor in potential savings from reduced construction time and operational efficiencies to create a comprehensive budget that reflects the financial viability of your project.
3. Designing Your Modular Building
Architectural Considerations
Designing a modular building involves unique considerations. Modular structures can be customized to suit various architectural styles, but it’s essential to account for the modular nature of the construction. Work closely with architects and modular design specialists to optimize the design for efficient manufacturing and assembly while ensuring the building meets your aesthetic preferences.
Customization Options
One of the strengths of modular construction is its flexibility. Explore customization options to tailor your building to specific needs. From layout variations to exterior finishes, modular construction allows for a high degree of personalization. Take advantage of this flexibility to create a space that aligns perfectly with your vision.
4. Manufacturing the Modules
Factory Production
Modular construction modules are fabricated in a controlled factory environment using advanced machinery and skilled labor. The precision-engineered modules undergo rigorous quality control checks at every stage of production. This ensures consistency and adherence to design specifications, ultimately resulting in modules that are of higher quality compared to traditional on-site construction.
Quality Control
Quality control is a cornerstone of modular construction. Each module undergoes thorough inspections throughout the manufacturing process. This includes testing for structural integrity, material quality, and compliance with safety standards. The stringent quality control measures contribute to the overall durability and reliability of modular construction projects.
5. Shipping and On-Site Assembly
Logistics
Efficient logistics are critical for the success of a modular construction project. Coordinate the transportation of modules to the construction site to minimize delays and ensure modules arrive in optimal condition. Working with experienced logistics professionals helps streamline the process, from loading modules at the factory to their timely arrival on-site.
On-Site Assembly
On-site assembly involves coordinating the placement and connection of modules to create the final structure. Skilled professionals, including crane operators and assembly teams, work together to ensure modules are securely positioned and integrated seamlessly. The efficiency of on-site assembly is a key factor in realizing the time and cost savings associated with modular construction.
6. Finishing Touches and Final Inspection
Interior and Exterior Finishes
Modular construction allows for a wide range of interior and exterior finishes to achieve the desired aesthetic. Interior finishes, such as flooring, walls, and fixtures, can be customized to meet specific design preferences. Exterior finishes, including cladding and roofing, contribute to the building’s visual appeal. Careful selection of finishes ensures the modular construction project meets both functional and aesthetic requirements.
Final Inspection
Before handing over the completed project, conduct a comprehensive final inspection. This includes a detailed review of the entire structure to confirm that all modules are correctly installed and connected. Check for any finishing discrepancies and ensure that the building meets safety and quality standards. The final inspection is a crucial step in delivering a modular construction project that exceeds expectations.
Get Started on Your Project Today
No matter the project, Pacific Mobile Structures has the power to turn your vision into reality. Large enough to deliver on big, custom modular construction projects, but family owned and privately held. That means you’ll never catch us cutting corners or compromising on service to please shareholders. Our team of experienced professionals will guide you every step of the way, offering expertise in design, manufacturing, logistics, and on-site assembly. When you choose Pacific Mobile Structures, you’re partnering with a team committed to delivering high-quality, customized solutions that meet your unique project requirements.