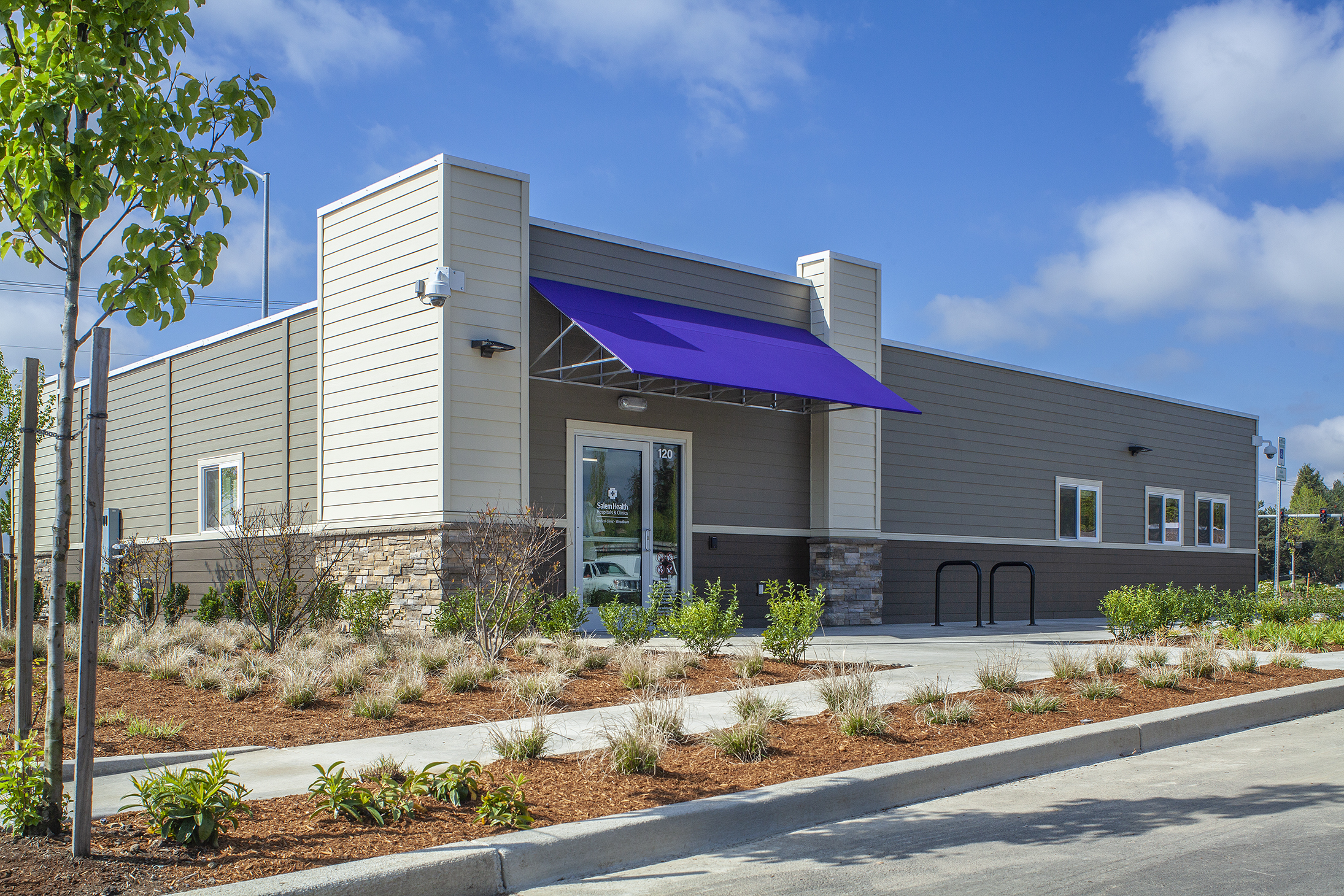
From Concept to Completion: Understanding the Modular Construction Process in Nevada
The modular construction process is revolutionizing the building industry in Nevada by offering a faster, more cost-effective, and environmentally friendly alternative to traditional construction. With clearly defined stages, modular construction ensures efficiency and high standards of quality from start to finish. Let’s take a closer look at each phase of this innovative process:
1. Initial Consultation
The journey begins with an initial consultation where clients discuss their project needs, goals, and budget with a modular construction expert. This step establishes a strong foundation for the project, enabling the team to understand the client’s vision and constraints. Whether the project involves a commercial building, an educational facility, or a residential development, this stage is crucial for aligning expectations and setting realistic timelines.
2. Design Phase
Once the project scope is defined, the design phase begins. Modular construction leverages advanced tools like Building Information Modeling (BIM) to create detailed and customizable plans. BIM allows stakeholders to visualize the final product, make adjustments in real-time, and detect potential issues early in the process. This collaborative approach ensures that the design meets the client’s specifications while adhering to local building codes and regulations. Additionally, modular designs are inherently flexible, enabling clients to choose from a variety of layouts, finishes, and features.
3. Off-Site Manufacturing
One of the hallmarks of modular construction is the off-site manufacturing process. Modules are built in a controlled factory environment using state-of-the-art machinery and standardized procedures. This setting minimizes exposure to weather-related delays and ensures precision in every component. The controlled environment also reduces material waste, making this phase not only efficient but also environmentally sustainable. During this stage, quality control measures are rigorously applied to guarantee that each module meets or exceeds industry standards.
4. Site Preparation
While the modules are being constructed off-site, site preparation occurs simultaneously, significantly shortening the overall project timeline. Site preparation involves tasks such as clearing the land, laying foundations, and setting up utility connections. By running these processes concurrently, modular construction can achieve completion timelines that are up to 50% faster than traditional methods.
5. Delivery and Assembly
Once the modules are ready, they are transported to the project site for assembly. Specialized equipment and experienced crews ensure that the modules are seamlessly joined together. This phase is completed in a matter of days, minimizing disruptions to the surrounding community. The modular units are designed to integrate perfectly, creating a finished structure that is indistinguishable from conventionally built buildings.
6. Final Inspection and Handover
The final stage involves thorough inspections to ensure the building complies with all local codes and regulations. Finishing touches, such as interior and exterior detailing, are added during this phase. Once everything is approved, the project is handed over to the client, ready for immediate use.
Why Choose Modular Construction in Nevada?
Nevada’s diverse landscape and growing economy make modular construction an ideal choice for a variety of projects. The streamlined process reduces labor costs and construction timelines, allowing businesses and communities to meet their building needs efficiently. Additionally, modular construction’s sustainable practices align with Nevada’s increasing focus on environmental stewardship.
Whether you’re planning a new office, a school, or a healthcare facility, modular construction provides a reliable and innovative solution. From concept to completion, this process ensures a seamless and satisfying experience for clients and stakeholders alike.